Essential Guide to Industrial Electronic Equipment Applications
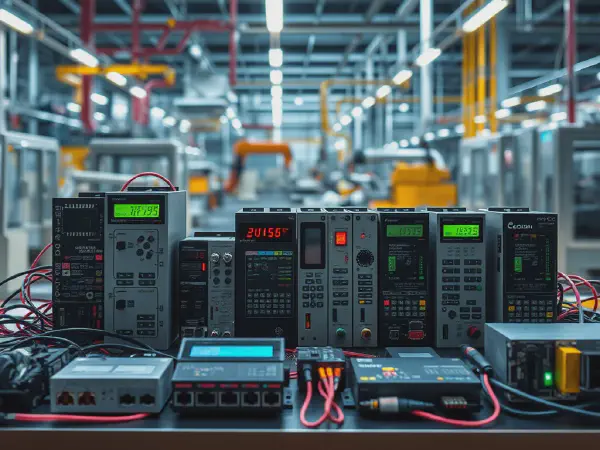
Understanding Industrial Electronic Equipment: The Backbone of Modern Industry
Industrial Electronic Equipment is a vital component in the automation and control of industrial processes. These devices include sensors, controllers, actuators, and other electronic components that help monitor and manage machinery and production lines. The integration of these electronic systems has revolutionized the manufacturing landscape, ensuring higher accuracy, efficiency, and safety in operations.
The reliability of a fanless industrial pc ensures minimal maintenance and longer lifespan in demanding environments.
The range of Industrial Electronic Equipment is vast, catering to various industries such as manufacturing, energy, transportation, and telecommunications. With advancements in technology, these devices have evolved from standalone equipment to interconnected systems that communicate and collaborate in real-time. This evolution has paved the way for the Industrial Internet of Things (IIoT), where equipment can share data and insights to optimize performance and reduce downtime.
One of the major advantages of Industrial Electronic Equipment is its ability to enhance productivity through automation. By employing electronic devices for control and monitoring, industries can minimize human error, streamline processes, and ensure consistent quality of output. Additionally, these systems can collect valuable performance data that can be analyzed for continuous improvement in operations.
Moreover, Industrial Electronic Equipment plays a critical role in maintaining safety standards within industrial environments. With features such as emergency shut-off systems, alarms, and real-time monitoring, these devices help mitigate risks associated with machinery and electrical setups. Implementing robust electronic solutions not only protects workers but also prolongs the lifespan of equipment.
In conclusion, Industrial Electronic Equipment is integral to modern manufacturing and industrial operations. As technology continues to evolve, industries must adapt to harness the full potential of these systems to remain competitive in an ever-changing market.
Applications of Industrial Electronic Equipment
Control systems for automation are a prominent application of Industrial Electronic Equipment. These systems utilize programmable logic controllers (PLCs) and distributed control systems (DCS) to automate machinery and processes, allowing for increased precision and efficiency in production lines.
In the competitive market, sourcing an industrial pc australia can streamline operations and boost efficiency across various sectors.
Measurement and sensing devices are critical for monitoring environmental conditions and operational parameters. Sensors measure variables such as temperature, pressure, and flow, providing real-time data to control systems and ensuring that processes operate within specified limits.
Choosing an industrial fanless pc is essential for noise-sensitive applications where silence enhances productivity.
Industrial robotics and machinery represent another significant application of Industrial Electronic Equipment. Robots equipped with advanced sensors and controllers perform tasks such as welding, painting, and assembly with high levels of speed and precision, transforming the landscape of manufacturing.
Process control in manufacturing heavily relies on various electronic devices to regulate and optimize production parameters. This includes the use of controllers that adjust inputs to maintain desired output levels, ensuring quality and efficiency in production.
Energy management systems utilize Industrial Electronic Equipment to monitor and control energy consumption across industrial facilities. These systems integrate smart meters, sensors, and controllers to promote energy efficiency and reduce operational costs.
Maintenance of Industrial Electronic Equipment
Routine inspection and preventive maintenance are crucial for ensuring the reliability and functionality of Industrial Electronic Equipment. Regular checks can identify potential issues before they escalate, minimizing downtime and repair costs.
Troubleshooting common issues involves diagnosing problems within electronic systems, which may include software glitches or hardware failures. Having a structured approach to troubleshooting can significantly improve response times and restore operations promptly.
Upgrading and retrofitting equipment is essential for industries looking to enhance performance and adopt new technologies. By integrating the latest electronic solutions, businesses can improve efficiency and adapt to changing industry demands.
The importance of calibration and testing cannot be overstated, as accurate measurements are vital for the reliability of Industrial Electronic Equipment. Regular calibration ensures that devices operate within predefined limits, providing trustworthy data for operational decisions.
Best practices for equipment longevity include maintaining a clean environment, monitoring performance metrics, and following manufacturer guidelines for usage and maintenance. A proactive approach to equipment care not only extends lifespan but also enhances overall performance.
Networking and Communication in Industrial Electronics
Industrial Internet of Things (IIoT) technologies are central to the evolution of networking in Industrial Electronics. IIoT enables the interconnection of devices, allowing for data exchange that leads to improved decision-making and operational efficiency.
Protocols used in industrial networks, such as Modbus, Profibus, and Ethernet/IP, facilitate communication between devices. These standard protocols ensure compatibility and interoperability across various systems, enhancing operational flexibility.
Remote monitoring and control systems are increasingly prevalent, allowing operators to manage processes and equipment from distant locations. This capability enhances responsiveness and operational efficiency, especially in large facilities or multiple sites.
Cybersecurity in industrial communications has become a critical concern as connectivity increases. Implementing robust security measures protects against cyber threats that could disrupt operations or compromise sensitive data.
Wired vs. wireless communication methods offer different advantages in industrial settings. While wired connections typically provide reliability and stability, wireless solutions offer flexibility and ease of installation in complex environments.
Future Trends in Industrial Electronic Equipment
Advances in smart sensors and actuators are likely to drive significant changes in Industrial Electronic Equipment. These devices are becoming more capable of intelligent decision-making, leading to more autonomous and adaptive systems in industrial environments.
Integration of AI and machine learning into Industrial Electronic Equipment will enhance data analysis and predictive maintenance capabilities. By leveraging AI, industries can optimize processes dynamically and minimize downtime through proactive maintenance strategies.
Sustainability practices in electronic equipment are gaining momentum as industries strive to reduce their environmental footprints. Innovations in energy-efficient devices and sustainable materials are becoming pivotal in shaping future industrial practices.
The impact of 5G on industrial automation will be transformative, enabling faster, more reliable communications between devices. This advancement is expected to facilitate real-time data sharing, further enhancing the capabilities of automated systems.
The rise of modular and flexible equipment designs will allow industries to adapt quickly to changing demands. Modular systems enable easy upgrades and modifications, keeping operations resilient and competitive in a dynamic marketplace.
Safety Standards for Industrial Electronic Equipment
Essential safety regulations and guidelines, such as ISO 13849 and IEC 61508, govern the design and operation of Industrial Electronic Equipment. Adhering to these standards ensures devices are safe, reliable, and meet specific performance requirements.
Risk assessment procedures are integral to developing a safety strategy for industrial environments. Conducting thorough assessments identifies potential hazards and informs the design and implementation of safety measures within equipment.
Emergency stop systems and measures are critical components designed to halt machinery operations during hazardous situations. Implementing these systems effectively protects workers and minimizes the risk of equipment damage.
Training for safe equipment handling is vital for all personnel involved in industrial operations. Comprehensive training programs promote awareness of risks and the proper use of Industrial Electronic Equipment, fostering a culture of safety.
Compliance with international safety standards is essential for industries operating at a global scale. Meeting these standards not only ensures safety but also enhances credibility and competitive advantage in the international market.